Precision by tradition
Synchronous motors make grinding spindles more economical and efficient
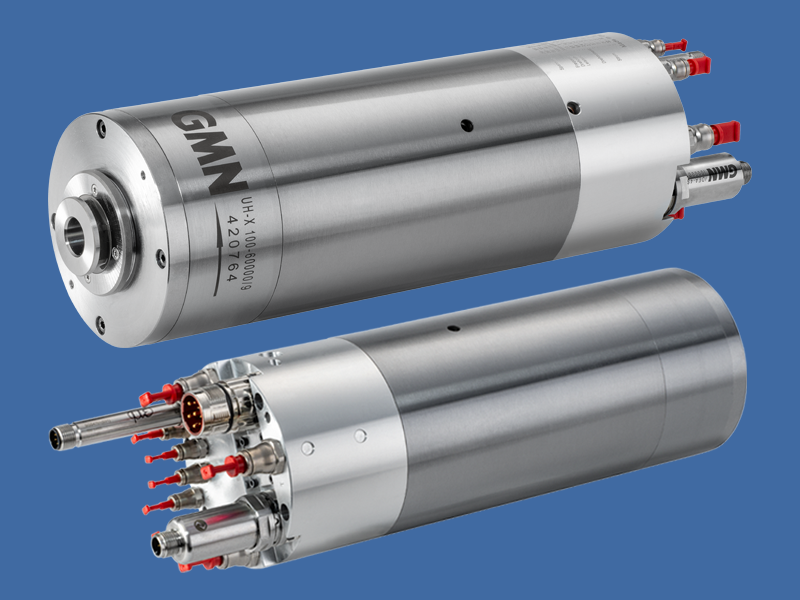
The new, resource-saving UH grinding spindles from GMN enable greater productivity and production quality. They achieve their high efficiency thanks to the synchronous drive used for the first time. Thanks to the IDEA-4S embedded system, they are also the first IIoT-capable models as standard. This makes them part of an overall concept for the digitalization of spindle technology for milling and grinding machines.
Dr. Jens Falker, Head of Engineering Spindle Technology at GMN, believes that the installed power of many spindles is oversized for the majority of applications. The possible peak loads are often only reached for a short time. “This is a nuisance, because under partial load the drives do not work at their optimum and consume an unnecessary amount of resources.”
This phenomenon often occurs with drives with asynchronous motors. For this reason, GMN prefers to use synchronous drives for the new UH spindles. There are two variants:
- Synchronous motors with internal magnets (IPM) are used for models in the medium speed range.
- If faster rotations are required, permanent magnet synchronous motors (PM) are chosen.
Synchronous motors manage with a third of the installed power
The difference to asynchronous motors is particularly evident in the IPM versions. As they enable a higher torque, they make better use of the available power during machining. According to Dr. Falker, spindles that manage with a third less installed power are therefore sufficient for most applications.
To illustrate the difference, he compares two drives with each other. An HV-X 120 45000/18 spindle with asynchronous motor, 120 mm spindle housing, maximum 45,000 rpm and 15 kW S1 power is entered into the race. A UH-X 120 45000/10 spindle with a synchronous motor and otherwise the same data will also be competing. However, this only requires a continuous output of 10 kW. An HSK-40 tool system is used for both spindles.
As an example, Dr. Falker selects three common machining situations for grinding: at 25,000 rpm, 36,000 rpm and 44,000 rpm.
In all three applications, only the UH spindle is above the partial load range. It is even close to the full load line in the two machining situations at 36,000 rpm and 44,000 rpm.
The HV-X spindle equipped with an asynchronous motor moves either in the partial load range or only slightly above it. “This shows that the synchronously driven UH spindles make much better use of the power range and achieve a higher level of efficiency,” emphasizes the Head of Engineering Spindle Technology.
Higher cutting speeds and better machining quality
There is also another advantage: the IPM motors of the synchronous drives allow for larger axle holes, ball bearings and shaft diameters; the difference is usually one bearing bore size.
“Thanks to the higher power density, we can use more compact assemblies and shorter shafts with smoother running,” explains Dr. Falker. The result: the maximum vibration speed has been reduced to 0.7 mm/s, compared to 1.12 mm/s for the previous HV spindle series.
The improved dynamic rigidity and load capacity of the spindle result in two possible applications: Compared to asynchronous motors, either larger tool interfaces or higher critical speeds can be used with the same shaft. The result: Higher cutting speeds are possible, productivity increases and the quality of the grinding process improves.
Smaller spindle system saves resources
The reduction in power consumption and energy consumption has a significant effect on the overall system consisting of spindle, inverter and control cabinet. The components can be dimensioned smaller, and a motor choke is even superfluous in many cases.
For example, while an HV spindle with an asynchronous motor requires 41 A nominal current, a UH spindle with a synchronous motor requires only 24 A. A correspondingly smaller power module can therefore be installed. At the same time, the rotor heats up less and the temperature remains below 100 ºC - compared to 200 ºC with a conventional spindle. This has a doubly positive effect: The thermal displacement of the shaft is reduced, it requires less cooling, while the machining quality increases.
The smaller systems not only reduce energy requirements. The new UH models also require less compressed air and a smaller amount of lubricating oil and work more quietly. This is confirmed by systematic comparisons between a UH-X 100 - 60000/9 and the asynchronously driven predecessor model HV-X 100 - 60000/9.
In the tests, the new spindle type consumed around 35 percent less air, and the savings in oil consumption were even slightly higher. With the new product, whose bearing diameter is one index larger, the noise level was 12 dB lower at its peak. Another advantage: the innovation showed an improved sealing effect against oil leakage in all installation positions.
In addition, the new spindles can report their own oil requirements to suitable lubrication units. The IIoT-capable top model PRELUB GPi PLUS from the latest GMN series even automatically supplies the spindle with the required amount of lubricant.
Spindle becomes part of the digital factory
“With our new UH series, we are making the machine tool spindle ready for the digital factory,” explains Dr. Falker. This is why the new models are equipped with the IIoT technology IDEA-4S as standard for the first time, which enables them to communicate and network comprehensively in line with Industry 4.0.
The name of the embedded system developed by GMN stands for “integrated data acquisition and evaluation for spindles”. Thanks to its intelligent sensor technology, it permanently records the most important process values and evaluates them while they are still in the spindle. It also reports this information via a bidirectional signal via IO-Link to the machine controller and the production networks. “In this way, the user is constantly informed about how his spindle is behaving, so he can optimize its use immediately,” explains the engineer.
Online tool complements IIoT connection
GMN is continuing its digitalization on the web. With the online software tool SpiOnline, customers can determine the optimum tool-spindle combination for their grinding process in advance of machining and thus optimize their production independently.
On the one hand, they can search for the best tool for an existing spindle, for example to achieve a specific speed range and an optimum machining result. On the other hand, they can determine the right spindle for a specific application with a tool to be used.
Synchronously driven grinding spindles in four sizes
The new synchronously driven models are available in the variants UH-X for internal grinding and UH-P for grinding and milling applications with HSK interfaces for manual tool changes. There are four sizes each with sleeve diameters of 100, 120, 150 and 170 mm. Depending on the model, the power ratings range up to 32 kW and the speeds up to a maximum of 120,000 rpm.
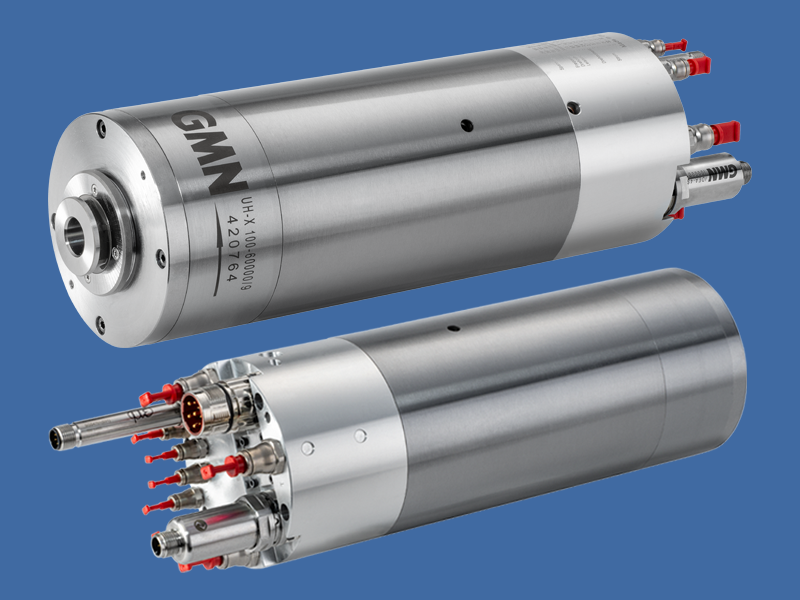
The new, resource-saving UH grinding spindles from GMN enable greater productivity and production quality. They achieve their high efficiency thanks to the synchronous drive used for the first time. Thanks to the IDEA-4S embedded system, they are also the first IIoT-capable models as standard. This makes them part of an overall concept for the digitalization of spindle technology for milling and grinding machines.
Dr. Jens Falker, Head of Engineering Spindle Technology at GMN, believes that the installed power of many spindles is oversized for the majority of applications. The possible peak loads are often only reached for a short time. “This is a nuisance, because under partial load the drives do not work at their optimum and consume an unnecessary amount of resources.”
This phenomenon often occurs with drives with asynchronous motors. For this reason, GMN prefers to use synchronous drives for the new UH spindles. There are two variants:
- Synchronous motors with internal magnets (IPM) are used for models in the medium speed range.
- If faster rotations are required, permanent magnet synchronous motors (PM) are chosen.
Synchronous motors manage with a third of the installed power
The difference to asynchronous motors is particularly evident in the IPM versions. As they enable a higher torque, they make better use of the available power during machining. According to Dr. Falker, spindles that manage with a third less installed power are therefore sufficient for most applications.
To illustrate the difference, he compares two drives with each other. An HV-X 120 45000/18 spindle with asynchronous motor, 120 mm spindle housing, maximum 45,000 rpm and 15 kW S1 power is entered into the race. A UH-X 120 45000/10 spindle with a synchronous motor and otherwise the same data will also be competing. However, this only requires a continuous output of 10 kW. An HSK-40 tool system is used for both spindles.
As an example, Dr. Falker selects three common machining situations for grinding: at 25,000 rpm, 36,000 rpm and 44,000 rpm.
In all three applications, only the UH spindle is above the partial load range. It is even close to the full load line in the two machining situations at 36,000 rpm and 44,000 rpm.
The HV-X spindle equipped with an asynchronous motor moves either in the partial load range or only slightly above it. “This shows that the synchronously driven UH spindles make much better use of the power range and achieve a higher level of efficiency,” emphasizes the Head of Engineering Spindle Technology.
Higher cutting speeds and better machining quality
There is also another advantage: the IPM motors of the synchronous drives allow for larger axle holes, ball bearings and shaft diameters; the difference is usually one bearing bore size.
“Thanks to the higher power density, we can use more compact assemblies and shorter shafts with smoother running,” explains Dr. Falker. The result: the maximum vibration speed has been reduced to 0.7 mm/s, compared to 1.12 mm/s for the previous HV spindle series.
The improved dynamic rigidity and load capacity of the spindle result in two possible applications: Compared to asynchronous motors, either larger tool interfaces or higher critical speeds can be used with the same shaft. The result: Higher cutting speeds are possible, productivity increases and the quality of the grinding process improves.
Smaller spindle system saves resources
The reduction in power consumption and energy consumption has a significant effect on the overall system consisting of spindle, inverter and control cabinet. The components can be dimensioned smaller, and a motor choke is even superfluous in many cases.
For example, while an HV spindle with an asynchronous motor requires 41 A nominal current, a UH spindle with a synchronous motor requires only 24 A. A correspondingly smaller power module can therefore be installed. At the same time, the rotor heats up less and the temperature remains below 100 ºC - compared to 200 ºC with a conventional spindle. This has a doubly positive effect: The thermal displacement of the shaft is reduced, it requires less cooling, while the machining quality increases.
The smaller systems not only reduce energy requirements. The new UH models also require less compressed air and a smaller amount of lubricating oil and work more quietly. This is confirmed by systematic comparisons between a UH-X 100 - 60000/9 and the asynchronously driven predecessor model HV-X 100 - 60000/9.
In the tests, the new spindle type consumed around 35 percent less air, and the savings in oil consumption were even slightly higher. With the new product, whose bearing diameter is one index larger, the noise level was 12 dB lower at its peak. Another advantage: the innovation showed an improved sealing effect against oil leakage in all installation positions.
In addition, the new spindles can report their own oil requirements to suitable lubrication units. The IIoT-capable top model PRELUB GPi PLUS from the latest GMN series even automatically supplies the spindle with the required amount of lubricant.
Spindle becomes part of the digital factory
“With our new UH series, we are making the machine tool spindle ready for the digital factory,” explains Dr. Falker. This is why the new models are equipped with the IIoT technology IDEA-4S as standard for the first time, which enables them to communicate and network comprehensively in line with Industry 4.0.
The name of the embedded system developed by GMN stands for “integrated data acquisition and evaluation for spindles”. Thanks to its intelligent sensor technology, it permanently records the most important process values and evaluates them while they are still in the spindle. It also reports this information via a bidirectional signal via IO-Link to the machine controller and the production networks. “In this way, the user is constantly informed about how his spindle is behaving, so he can optimize its use immediately,” explains the engineer.
Online tool complements IIoT connection
GMN is continuing its digitalization on the web. With the online software tool SpiOnline, customers can determine the optimum tool-spindle combination for their grinding process in advance of machining and thus optimize their production independently.
On the one hand, they can search for the best tool for an existing spindle, for example to achieve a specific speed range and an optimum machining result. On the other hand, they can determine the right spindle for a specific application with a tool to be used.
Synchronously driven grinding spindles in four sizes
The new synchronously driven models are available in the variants UH-X for internal grinding and UH-P for grinding and milling applications with HSK interfaces for manual tool changes. There are four sizes each with sleeve diameters of 100, 120, 150 and 170 mm. Depending on the model, the power ratings range up to 32 kW and the speeds up to a maximum of 120,000 rpm.