Precision by tradition
GMN’s new Assembly Centre: flexible and efficient down to batch sizes of one
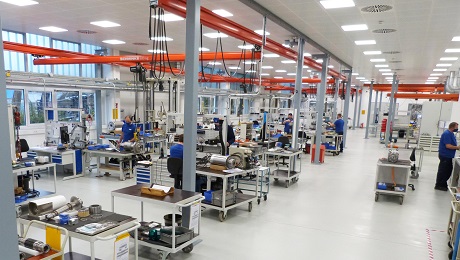
So far, long delivery times have been the downside of GMN machine spindles’ global success. This is because customer-specific small-series production, with its wide range of variants, requires time-consuming assembly in the cleanroom. To speed things up, the company decided at the end of 2018 to build a new Assembly Centre with an area of around 1,300 square metres. Working together with the employees, every process and all the workplaces have been optimised. Since the summer of 2020, the drive units have now been installed in the new assembly rooms in a paperless, flexible and efficient manner.
“Any product with a shaft, a housing and a spindle bearing from GMN can be assembled in the new Assembly Centre,” says Dr Edgar Verlemann, Managing Director of Technology, describing the aspirations for the new premises. In addition to new spindles for machine tools – especially for grinding and milling applications – generators, compressors and drive motors for mechanical and plant engineering are also being assembled there. Moreover, components for the GMN service area can be repaired there at any time.
GMN manufactures only part of its grinding spindles based on its known catalogue range. Due to their numerous equipment options, around 60% of the spindle units are produced to meet specific customer requirements. The average batch size is five items per order, and around 6,000 units are produced each year. With orders growing steadily over recent years until the 2020 corona crisis, assembly, with its mature structures, was coming close to its performance limits. Too many orders needed to be processed in parallel, leading to unwanted waiting times.
GMN wants to deliver fast-growing products more quickly
GMN has been using the coronavirus crisis to reposition itself. Dr Verlemann explains: “This means that we are simplifying, flexibilising and accelerating the production of customised products that have particularly high growth rates. This way, we can plan the assembly of different models and designs more easily and master them reliably.”
Since the site in northern Nuremberg, where GMN has been headquartered for 113 years, is highly built up, the management decided to convert an existing building. Accordingly, the departments housed there, such as GMN’s sealing ring production, first had to be relocated. This was done by the middle of 2019. Then, the old building was extensively equipped with a sustainable air conditioning system.
Flexible use instead of fixed workplaces
What is new is the way that rigid job descriptions have been dispensed with. Whereas previously, the employees specialised in individual spindle types, now all of them have the knowledge to assemble the entire product range. The concept also means that everyone now has their own trolley with their own tools. This means that it can now be used at different workstations, where the assembly capacity is currently required.
Empty paths and unnecessary downtimes, as well as stressful short assignments, are now avoided; the technicians can work in a more concentrated way and at the same time continuously. “This gives us a great deal of flexibility, and we operate with a planned lead time in assembly,” Dr Verlemann adds.
Paperless assembly
Paper-based assembly drawings are nowhere to be found in the Assembly Centre. Instead, each workstation is equipped with touchscreens on which the current drawings can be called up at any time. “Digitisation, with paperless assembly, simplifies work and is well received by our department,” reports Wolfgang Gantke, Head of Assembly.
GMN has divided the Assembly Centre into several areas for optimal material and process flow: Initial cleaning, in which the material required is cleaned, then the picking and preparation for the individual batches, followed by the actual assembly, the inlet and test area and, last of all, quality assurance.
Cleanroom manufacturing
On arrival, the materials are first cleaned. Before moving on to the next department, they must pass through an airlock to the cleanroom, which protects the assembly area from dirt particles. Since impurities affect both the drives’ quality and their service lives, GMN has developed a consistent cleanroom concept for the new premises.
“We strive for the highest level of cleanliness in the assembly area when installing high-precision GMN spindle bearings. We have developed a modern and sustainable concept for this, which ensures that employees behave in the working environment concerned in such a way that the highest particle minimisation demands are met when assembling components. And this is without the cost of a sophisticated cleanroom,” says Managing Director Dr Verlemann as he explains the decision.
Tightest tolerances below 1 µm
Just as the materials enter the cleanroom having been cleaned, employees enter the Assembly Centre with fresh working clothes, which they receive from GMN.
The materials for each order are put together behind the airlock. Mechanical components arrive in blue boxes, electrical ones in yellow. The cables are pre-assembled. Then, all the materials needed to assemble an order are loaded onto a small transport trolley, on which the order starts its journey through the Assembly Centre.
Then it’s on to the mechatronic assembly of the components. Top precision is one of the hallmarks of GMN drive units. Managing Director Dr Edgar Verlemann puts it like this: “Many manufacturers offer precisely working spindles. But if the tightest tolerances of <1 µm are required for concentricity, for example, for a workpiece spindle, there are few other who can compete. We only have a few competitors in the market.” The ball bearings produced by GMN in Nuremberg, exclusively installed in the Assembly Centre, are also essential for product quality.
High-performance spindles ready for Industry 4.0
After all the assembly operation have been completed, the drive unit is tested under practical conditions. To this end, the technicians simulate a machine operation with 120 switching cycles for an automatic tool changing system, for example. In the test room and during quality assurance, the geometry is examined for the smallest deviations with a 3D measuring machine. In addition, the temperature, pressures, flow rates, motors and sensors are monitored.
The Assembly Centre is designed for future needs, Dr Verlemann adds: “Of course, we can also check electronic components, sensors and the IO-link interfaces of the new IoT-capable high-performance spindles with our own IDEA-4S digital interface.”
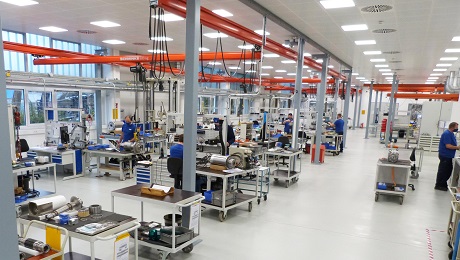
So far, long delivery times have been the downside of GMN machine spindles’ global success. This is because customer-specific small-series production, with its wide range of variants, requires time-consuming assembly in the cleanroom. To speed things up, the company decided at the end of 2018 to build a new Assembly Centre with an area of around 1,300 square metres. Working together with the employees, every process and all the workplaces have been optimised. Since the summer of 2020, the drive units have now been installed in the new assembly rooms in a paperless, flexible and efficient manner.
“Any product with a shaft, a housing and a spindle bearing from GMN can be assembled in the new Assembly Centre,” says Dr Edgar Verlemann, Managing Director of Technology, describing the aspirations for the new premises. In addition to new spindles for machine tools – especially for grinding and milling applications – generators, compressors and drive motors for mechanical and plant engineering are also being assembled there. Moreover, components for the GMN service area can be repaired there at any time.
GMN manufactures only part of its grinding spindles based on its known catalogue range. Due to their numerous equipment options, around 60% of the spindle units are produced to meet specific customer requirements. The average batch size is five items per order, and around 6,000 units are produced each year. With orders growing steadily over recent years until the 2020 corona crisis, assembly, with its mature structures, was coming close to its performance limits. Too many orders needed to be processed in parallel, leading to unwanted waiting times.
GMN wants to deliver fast-growing products more quickly
GMN has been using the coronavirus crisis to reposition itself. Dr Verlemann explains: “This means that we are simplifying, flexibilising and accelerating the production of customised products that have particularly high growth rates. This way, we can plan the assembly of different models and designs more easily and master them reliably.”
Since the site in northern Nuremberg, where GMN has been headquartered for 113 years, is highly built up, the management decided to convert an existing building. Accordingly, the departments housed there, such as GMN’s sealing ring production, first had to be relocated. This was done by the middle of 2019. Then, the old building was extensively equipped with a sustainable air conditioning system.
Flexible use instead of fixed workplaces
What is new is the way that rigid job descriptions have been dispensed with. Whereas previously, the employees specialised in individual spindle types, now all of them have the knowledge to assemble the entire product range. The concept also means that everyone now has their own trolley with their own tools. This means that it can now be used at different workstations, where the assembly capacity is currently required.
Empty paths and unnecessary downtimes, as well as stressful short assignments, are now avoided; the technicians can work in a more concentrated way and at the same time continuously. “This gives us a great deal of flexibility, and we operate with a planned lead time in assembly,” Dr Verlemann adds.
Paperless assembly
Paper-based assembly drawings are nowhere to be found in the Assembly Centre. Instead, each workstation is equipped with touchscreens on which the current drawings can be called up at any time. “Digitisation, with paperless assembly, simplifies work and is well received by our department,” reports Wolfgang Gantke, Head of Assembly.
GMN has divided the Assembly Centre into several areas for optimal material and process flow: Initial cleaning, in which the material required is cleaned, then the picking and preparation for the individual batches, followed by the actual assembly, the inlet and test area and, last of all, quality assurance.
Cleanroom manufacturing
On arrival, the materials are first cleaned. Before moving on to the next department, they must pass through an airlock to the cleanroom, which protects the assembly area from dirt particles. Since impurities affect both the drives’ quality and their service lives, GMN has developed a consistent cleanroom concept for the new premises.
“We strive for the highest level of cleanliness in the assembly area when installing high-precision GMN spindle bearings. We have developed a modern and sustainable concept for this, which ensures that employees behave in the working environment concerned in such a way that the highest particle minimisation demands are met when assembling components. And this is without the cost of a sophisticated cleanroom,” says Managing Director Dr Verlemann as he explains the decision.
Tightest tolerances below 1 µm
Just as the materials enter the cleanroom having been cleaned, employees enter the Assembly Centre with fresh working clothes, which they receive from GMN.
The materials for each order are put together behind the airlock. Mechanical components arrive in blue boxes, electrical ones in yellow. The cables are pre-assembled. Then, all the materials needed to assemble an order are loaded onto a small transport trolley, on which the order starts its journey through the Assembly Centre.
Then it’s on to the mechatronic assembly of the components. Top precision is one of the hallmarks of GMN drive units. Managing Director Dr Edgar Verlemann puts it like this: “Many manufacturers offer precisely working spindles. But if the tightest tolerances of <1 µm are required for concentricity, for example, for a workpiece spindle, there are few other who can compete. We only have a few competitors in the market.” The ball bearings produced by GMN in Nuremberg, exclusively installed in the Assembly Centre, are also essential for product quality.
High-performance spindles ready for Industry 4.0
After all the assembly operation have been completed, the drive unit is tested under practical conditions. To this end, the technicians simulate a machine operation with 120 switching cycles for an automatic tool changing system, for example. In the test room and during quality assurance, the geometry is examined for the smallest deviations with a 3D measuring machine. In addition, the temperature, pressures, flow rates, motors and sensors are monitored.
The Assembly Centre is designed for future needs, Dr Verlemann adds: “Of course, we can also check electronic components, sensors and the IO-link interfaces of the new IoT-capable high-performance spindles with our own IDEA-4S digital interface.”