Precision by tradition
GMN special bearings and bearing systems for customer-specific solutions
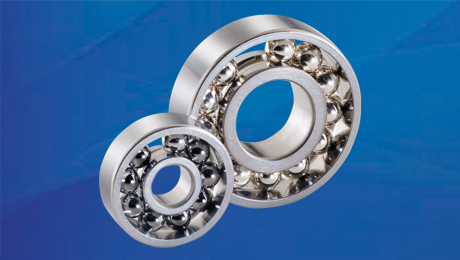
Very high-precision special ball bearings for challenging applications are a GMN speciality, alongside spindle and deep groove ball bearings. The mechanical engineering company from Nuremberg in Germany is always in demand when the requirements for speed, low vibration and running accuracy are particularly high. Or when bearings and bearing systems need to be used under extreme environmental conditions, in a vacuum or a cleanroom.
Regardless of whether the ball bearings are needed as touchdown bearings, or for use in blowers, compressors or vacuum pumps, or employed as complete bearing systems for X-ray tubes and laser applications, GMN offers special application-specific solutions for these and many other fields of application. The range of services begins with the development and production of individual ball bearings and integrated bearing systems including the shaft, conversion parts and the housing. It even goes as far as the all-round service for the subsequent delivery of series-manufactured parts, including the Kanban processing and stocking of the items on-site at the end customer. GMN focuses on spindle ball bearings, groove ball bearings and hybrid bearings with ceramic balls. Needle bearings, slide (plain) bearings and magnetic bearings do not form part of the product range.
A considerable effort
Custom-made products are always in demand when standard bearings do not fulfil customer requirements in terms of geometry, precision, material, tribological or operational requirements. For example, during product development, customers often discover that their specific wishes cannot be fulfilled with models out of the catalogue.
“The effort that we put into the design and construction of individual bearing systems and individual special ball bearings is considerable”, explains Stefan Tritthart: “Sometimes many components need to be optimised to meet individual requirements and environmental conditions. Depending on the intended use, specific materials and coatings may also be required, while internal processes may need to be modified and special tools procured.”
“Once the prototype has been successfully tested, we start manufacturing the new product in series”, explains Andreas Böhrer, technical sales staff member: “We do not offer pure single-item production, we achieve our sales through series production.”
Close collaboration far beyond the series production
An application engineer accompanies the customer through the entire development process as a permanent contact person. This service orientation is part of GMN’s philosophy, says Stefan Tritthart: “Our support is very comprehensive, and extends far beyond the series production of a special bearing or bearing system. Because we do not just sit back and put our feet up once the product has been completed and accepted. The project partners remain in close contact and thus continue the innovation cycle to further develop and optimise the series product. “
Numerous configuration options
The many configuration options for the product leave practically no wish unfulfilled. At the beginning, besides the area of application, the requirements in terms of precision, rigidity, operating temperature, resilience, speed, as well as shelf life and service life must all be clarified.
The type of bearing then must be determined. Which bearing design - “S” for robust, “SM” for high-speeds and “KH” for extremely high-speed applications – will be required? Should the cages be made of reinforced textile or polyether ether ketone (PEEK) reinforced with carbon-fibre? Are chrome steel balls and rings sufficient or would ceramics and special steels be the better choice? Which installation position, fastenings and dimensions are required? GMN offers internal diameters ranging from 5 to 120 mm. Which contact angles are required? Should it be rigid or spring-preloaded?
It is also necessary to define whether dry or direct oil lubrication or grease relubrication is needed and which bore position has been selected for the supply of media. The strength of the operational radial and axial loads to which the bearing is exposed also need to be considered. Finally, the other components such as the shaft, housing, associated components, springs, washers, snap (retaining) rings, seals and connection pieces, as well as the bearing attachment must be specified. Considering the numerous variants, most customers prefer to draw on the extensive experience of “their own” GMN application engineer.
Sample parts are manufactured under series conditions
Once all the requirements have been met and the bearing design has been agreed on, the production of the prototype can begin. “We already produce the sample parts under series conditions, and we can perform many manufacturing steps on our own premises thanks to our large manufacturing depth.”, Stefan Tritthart promises.
GMN manufactures a large proportion of the parts needed itself. Modern technologies such as CBN (cubic boron nitride) grinding and hard turning are used. Moreover, the company can draw on its own expertise and supplies from the business areas of machine spindles, freewheel clutches and seals. The components for vacuum applications are also plasma cleaned on-site and, where necessary, coated with silver, lead, gold or molybdenum disulphide on our PVD (physical vapour deposition) system. The bearings can also be assembled under cleanroom conditions. Our measuring device and precision measuring division - as an independent, in-house service provider - tests every quality-relevant component.
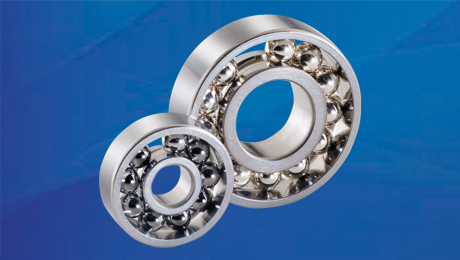
Very high-precision special ball bearings for challenging applications are a GMN speciality, alongside spindle and deep groove ball bearings. The mechanical engineering company from Nuremberg in Germany is always in demand when the requirements for speed, low vibration and running accuracy are particularly high. Or when bearings and bearing systems need to be used under extreme environmental conditions, in a vacuum or a cleanroom.
Regardless of whether the ball bearings are needed as touchdown bearings, or for use in blowers, compressors or vacuum pumps, or employed as complete bearing systems for X-ray tubes and laser applications, GMN offers special application-specific solutions for these and many other fields of application. The range of services begins with the development and production of individual ball bearings and integrated bearing systems including the shaft, conversion parts and the housing. It even goes as far as the all-round service for the subsequent delivery of series-manufactured parts, including the Kanban processing and stocking of the items on-site at the end customer. GMN focuses on spindle ball bearings, groove ball bearings and hybrid bearings with ceramic balls. Needle bearings, slide (plain) bearings and magnetic bearings do not form part of the product range.
A considerable effort
Custom-made products are always in demand when standard bearings do not fulfil customer requirements in terms of geometry, precision, material, tribological or operational requirements. For example, during product development, customers often discover that their specific wishes cannot be fulfilled with models out of the catalogue.
“The effort that we put into the design and construction of individual bearing systems and individual special ball bearings is considerable”, explains Stefan Tritthart: “Sometimes many components need to be optimised to meet individual requirements and environmental conditions. Depending on the intended use, specific materials and coatings may also be required, while internal processes may need to be modified and special tools procured.”
“Once the prototype has been successfully tested, we start manufacturing the new product in series”, explains Andreas Böhrer, technical sales staff member: “We do not offer pure single-item production, we achieve our sales through series production.”
Close collaboration far beyond the series production
An application engineer accompanies the customer through the entire development process as a permanent contact person. This service orientation is part of GMN’s philosophy, says Stefan Tritthart: “Our support is very comprehensive, and extends far beyond the series production of a special bearing or bearing system. Because we do not just sit back and put our feet up once the product has been completed and accepted. The project partners remain in close contact and thus continue the innovation cycle to further develop and optimise the series product. “
Numerous configuration options
The many configuration options for the product leave practically no wish unfulfilled. At the beginning, besides the area of application, the requirements in terms of precision, rigidity, operating temperature, resilience, speed, as well as shelf life and service life must all be clarified.
The type of bearing then must be determined. Which bearing design - “S” for robust, “SM” for high-speeds and “KH” for extremely high-speed applications – will be required? Should the cages be made of reinforced textile or polyether ether ketone (PEEK) reinforced with carbon-fibre? Are chrome steel balls and rings sufficient or would ceramics and special steels be the better choice? Which installation position, fastenings and dimensions are required? GMN offers internal diameters ranging from 5 to 120 mm. Which contact angles are required? Should it be rigid or spring-preloaded?
It is also necessary to define whether dry or direct oil lubrication or grease relubrication is needed and which bore position has been selected for the supply of media. The strength of the operational radial and axial loads to which the bearing is exposed also need to be considered. Finally, the other components such as the shaft, housing, associated components, springs, washers, snap (retaining) rings, seals and connection pieces, as well as the bearing attachment must be specified. Considering the numerous variants, most customers prefer to draw on the extensive experience of “their own” GMN application engineer.
Sample parts are manufactured under series conditions
Once all the requirements have been met and the bearing design has been agreed on, the production of the prototype can begin. “We already produce the sample parts under series conditions, and we can perform many manufacturing steps on our own premises thanks to our large manufacturing depth.”, Stefan Tritthart promises.
GMN manufactures a large proportion of the parts needed itself. Modern technologies such as CBN (cubic boron nitride) grinding and hard turning are used. Moreover, the company can draw on its own expertise and supplies from the business areas of machine spindles, freewheel clutches and seals. The components for vacuum applications are also plasma cleaned on-site and, where necessary, coated with silver, lead, gold or molybdenum disulphide on our PVD (physical vapour deposition) system. The bearings can also be assembled under cleanroom conditions. Our measuring device and precision measuring division - as an independent, in-house service provider - tests every quality-relevant component.