MASTERING PROCESSES
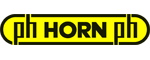
Every machining operation is a process: from grooving and parting off, to groove milling or face milling. These are processes that engineers perform every day and are stored as cycles in every machine control system. For this reason, HORN’s product portfolio boasts a huge selection of different tools. Furthermore, specialised machining processes such as gear skiving, bevel gear milling, thread whirling, brilliant-finish milling and turning, or speed forming require a high level of expertise in both tool technology and when it comes to process knowledge. For example, this expertise may involve the design of the tool cutting edges for whirling a multi-thread bone screw or the tooth profiles of gear hobs.
HORN has developed a set of speed-forming tools for machining grooves into cubic workpieces with maximum productivity. To create deep and narrow grooves (with a width of 2 mm (0.079") to 3 mm (0.118")), tool and mould makers generally use milling cutters with a large length-to-diameter ratio. Due to the high risk of breakage, relatively low feed rate and infeed settings have to be selected. But thanks to its tools, HORN allows you to create grooves with a depth of up to 20 mm (0.787") quickly and cost-effectively using the speed forming technique. The tools are based on the Supermini 105 system. As with broaching, the tool travels along a programmed path with a fixed tool spindle orientation. The maximum infeed for the individual strokes is 0.3 mm (0.012") with a fast feed rate setting (maximum 60 m/min (196.85 ft/min)).
Not only that, but the tool can also be combined with a cycle for producing curved or undulating grooves. This makes it a highly productive solution for creating cooling fins or reinforcing ribs on a casing, for example. When used with appropriate machines and components, the tools achieve shorter machining times because the droplet shape of the Supermini system is able to withstand higher bending loads, thereby allowing infeed in the longitudinal direction of cutting.
HORN has developed tools for the polygon turning process to manufacture non-circular contours. By adopting an axial feed, the tools enable you to produce non-circular contours on lathes consistently. This technique facilitates the production of polygon shapes, for example. During operation, the workpiece and tool axes are offset in relation to one another and a specific speed ratio is established between them. The tools are suitable for external and internal machining alike. Together, the axis offset, workpiece-to-tool speed ratio and circle of rotation of the cutting edge define the dimensions of the contour. Every tool system for polygon turning is individually tailored to the workpiece contour to be produced. The technique is highly suitable for series production processes because no jerky movements or reversals of motion occur during machining. HORN offers the polygon turning tool system in response to enquiries from customers who are looking to produce spline gears, polygons and other shapes in a cost-effective manner.
These are two examples of how HORN demonstrates that the company is there to support its users, not only as a pure precision tool manufacturer. With its expertise in tool manufacturing and extensive process knowledge, HORN sees itself as a problem solver, even when it comes to special machining solutions.