Open to your World
Primeras conferencias en Alemania sobre prensas servomecánicas para estampación en caliente
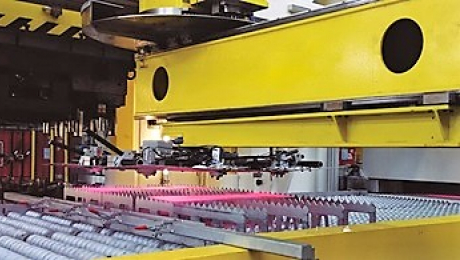
La tecnología servomecánica para estampación en caliente supone una revolución al mejorar la eficiencia energética, reducir el tiempo de ciclo e incrementar la fiabilidad
Dentro de la constante búsqueda de métodos innovadores en la fabricación de vehículos para lograr unidades cada vez más ligeras con las que adaptarse a las exhaustivas normas internacionales de emisiones, el estampado en caliente se configura como la técnica idónea para conformar metales con más alto límite elástico. Con este sistema se obtienen los niveles de seguridad requeridos y una reducción del peso de las piezas al lograr que sean más delgadas. Hasta la fecha, las prensas hidráulicas han sido la tecnología estándar en la estampación en caliente, llegando a dominar en solitario este terreno, si bien la reciente irrupción de las servomecánicas supone una revolución en este ámbito por los tres grandes beneficios que conllevan: la mejora de la eficiencia energética, la reducción del tiempo de ciclo y el incremento de la fiabilidad.
Los fabricantes son conscientes de que reducir las emisiones de carbono es una necesidad imperiosa. Dentro de este compromiso medioambiental, las prensas servomecánicas requieren de un consumo energético significativamente menor, ya que sólo consumen energía cuando el carro se encuentra en movimiento. Cuando la prensa está cerrada los servomotores no se mueven y, por tanto, no consumen energía.
La prensa servomecánica permite optimizar el movimiento y, en consecuencia, reducir el tiempo de ciclo. Su operatividad no depende de parámetros como el desgaste de los elementos, de modo que no se ve afectado el tiempo de reacción y la precisión de la pieza resultante. Y es que la servomecánica garantiza la precisión gracias a un innovador sistema de lazo cerrado de control que permite un mayor dinamismo. La simulación de un proceso tradicional de estampación en caliente permite constatar el aprovechamiento de la potencia instalada en la prensa servomecánica dado que la eficiencia del sistema de un motor servo es del 95,5% (en una prensa hidráulica convencional en situación de standby se puede desperdiciar hasta un 30% de la potencia instalada). En condiciones de trabajo óptimas se puede lograr hasta un 55% de reducción del consumo energético anual con la instalación de la conformación en caliente.
La fiabilidad de la tecnología de los servomotores está probada. Los sistemas mecánicos presentan de forma inherente menos problemas de mantenimiento, con lo que se limita el desgaste de los elementos y se evita un recambio frecuente de los mismos, favoreciendo así la producción. Los fabricantes de equipos originales de primer nivel indican que la necesidad de mantenimiento en las prensas mecánicas es de un 21% menor.
El fabricante de troqueles BATZ S Corp., con sede en Igorre (Bizkaia), junto al que Fagor Arrasate ha desarrollado la tecnología Hotteknik para estampación en caliente, cuenta en sus instalaciones con una prensa servomecánica de 15.000 kN para la conformación en caliente, tanto para pruebas de troquel como para la fabricación en pre-serie. La instalación se diseñó con una interfaz mixta que permite el control de la prensa servomecánica y proporciona al mismo tiempo la información necesaria para asegurar la compatibilidad con otra prensa hidráulica en parámetros como la velocidad, la fuerza o el perfil de carrera.
La estampación en caliente con prensas servomecánicas distingue a Fagor Arrasate del resto de competidores. Las innumerables bondades que ofrece la tecnología servomecánica serán expuestas a expertos y profesionales en un evento que tendrá lugar el 5 y 6 de julio en Langenfeld (Alemania) en la que será la primera presentación de los beneficios de esta técnica en el estampado en caliente en el país germano.
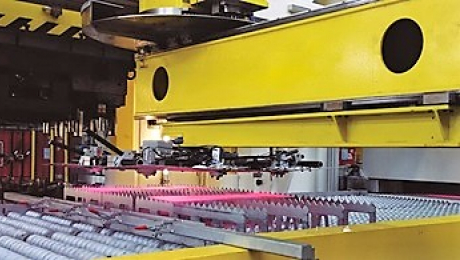
La tecnología servomecánica para estampación en caliente supone una revolución al mejorar la eficiencia energética, reducir el tiempo de ciclo e incrementar la fiabilidad
Dentro de la constante búsqueda de métodos innovadores en la fabricación de vehículos para lograr unidades cada vez más ligeras con las que adaptarse a las exhaustivas normas internacionales de emisiones, el estampado en caliente se configura como la técnica idónea para conformar metales con más alto límite elástico. Con este sistema se obtienen los niveles de seguridad requeridos y una reducción del peso de las piezas al lograr que sean más delgadas. Hasta la fecha, las prensas hidráulicas han sido la tecnología estándar en la estampación en caliente, llegando a dominar en solitario este terreno, si bien la reciente irrupción de las servomecánicas supone una revolución en este ámbito por los tres grandes beneficios que conllevan: la mejora de la eficiencia energética, la reducción del tiempo de ciclo y el incremento de la fiabilidad.
Los fabricantes son conscientes de que reducir las emisiones de carbono es una necesidad imperiosa. Dentro de este compromiso medioambiental, las prensas servomecánicas requieren de un consumo energético significativamente menor, ya que sólo consumen energía cuando el carro se encuentra en movimiento. Cuando la prensa está cerrada los servomotores no se mueven y, por tanto, no consumen energía.
La prensa servomecánica permite optimizar el movimiento y, en consecuencia, reducir el tiempo de ciclo. Su operatividad no depende de parámetros como el desgaste de los elementos, de modo que no se ve afectado el tiempo de reacción y la precisión de la pieza resultante. Y es que la servomecánica garantiza la precisión gracias a un innovador sistema de lazo cerrado de control que permite un mayor dinamismo. La simulación de un proceso tradicional de estampación en caliente permite constatar el aprovechamiento de la potencia instalada en la prensa servomecánica dado que la eficiencia del sistema de un motor servo es del 95,5% (en una prensa hidráulica convencional en situación de standby se puede desperdiciar hasta un 30% de la potencia instalada). En condiciones de trabajo óptimas se puede lograr hasta un 55% de reducción del consumo energético anual con la instalación de la conformación en caliente.
La fiabilidad de la tecnología de los servomotores está probada. Los sistemas mecánicos presentan de forma inherente menos problemas de mantenimiento, con lo que se limita el desgaste de los elementos y se evita un recambio frecuente de los mismos, favoreciendo así la producción. Los fabricantes de equipos originales de primer nivel indican que la necesidad de mantenimiento en las prensas mecánicas es de un 21% menor.
El fabricante de troqueles BATZ S Corp., con sede en Igorre (Bizkaia), junto al que Fagor Arrasate ha desarrollado la tecnología Hotteknik para estampación en caliente, cuenta en sus instalaciones con una prensa servomecánica de 15.000 kN para la conformación en caliente, tanto para pruebas de troquel como para la fabricación en pre-serie. La instalación se diseñó con una interfaz mixta que permite el control de la prensa servomecánica y proporciona al mismo tiempo la información necesaria para asegurar la compatibilidad con otra prensa hidráulica en parámetros como la velocidad, la fuerza o el perfil de carrera.
La estampación en caliente con prensas servomecánicas distingue a Fagor Arrasate del resto de competidores. Las innumerables bondades que ofrece la tecnología servomecánica serán expuestas a expertos y profesionales en un evento que tendrá lugar el 5 y 6 de julio en Langenfeld (Alemania) en la que será la primera presentación de los beneficios de esta técnica en el estampado en caliente en el país germano.
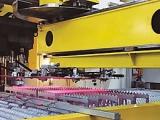