Eldec Quality Control: Control exhaustivo de la calidad para el templado inductivo
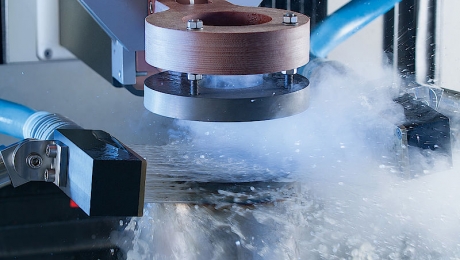
Los planificadores de la producción en la industria automotriz persiguen, cada vez más, una estrategia de "cero errores", en la medida en la que sea posible, ya que la complejidad técnica de los vehículos se ha incrementado enormemente en los últimos años. La consecuencia de ello son requisitos cada vez más exigentes, lo que supone un incremento del número de fuentes de error en la producción, como demuestran claramente las frecuentes campañas de llamada a taller de los últimos años. Esto hace necesario una monitorización de la calidad aún más amplia para muchos proveedores y fabricantes de equipos originales. Los procesos de tratamiento térmico también se ven especialmente afectados por ello, ya que tienen gran influencia en la estabilidad de componentes importantes. En este contexto, los especialistas en inducción de eldec renuevan su compromiso con todo lo relacionado con la monitorización de la calidad de las máquinas de templado inductivo: el "eldec Quality Control" abarca un paquete completo de nuevos ulos, con los que es posible optimizar la seguridad del proceso. Los componentes están basados los unos en los otros y se complementan. En combinación, garantizan a los usuarios un proceso de templado con una amplia monitorización.
Las cifras son cada vez más altas: de acuerdo con el instituto Center of Automotive Management (CAM) en Bergisch Gladbach, Alemania, solamente en EE. UU. se llamaron a taller más de 45 millones de vehículo el año pasado. "Problemas de seguridad", según el CAM, son la causa de ello. En dos años fue necesario comprobar y reparar en talleres más de 108 millones de vehículos en EE. UU. Esto supone enormes costos, los cuales tienen diferentes causas: los procesos de producción no seguros juegan aquí un papel central. El "eldec Quality Control" (eQC) sirve de ejemplo para evidenciar el esfuerzo que la ingeniería mecánica está haciendo para implantar un aseguramiento de la calidad a un nivel muy alto. Los especialistas de la inducción con sede en Dornstetten, cerca de Freudenstadt, Alemania, han dividido su paquete de medidas en dos áreas: "monitorización eléctrica" y "monitorización mecánica". Entre estas medidas se encuentran tres módulos completamente nuevos, los cuales contribuyen al aseguramiento de la calidad del proceso de templado: una detección de herramienta mediante un chip RFID, la medición continua de la tensión en el inductor y la monitorización del medio de enfriamiento brusco con ayuda de un sensor. "En total, mediante estas y otras medidas eQC se recoge una gran cantidad de datos, todos los cuales se guardan para compararlos con diferentes valores de referencia. En caso de desviaciones, la máquina informa del problema y detiene el proceso en determinadas circunstancias", explica Andreas Endmann, director del departamento de ventas tecnológicas para sistemas de templado de eldec. "Una mayor seguridad del proceso y una mejor monitorización de la calidad son casi impensables".
¿Se ha empleado la herramienta correcta?
La detección de herramientas sirve como ejemplo en la práctica: en el futuro, la máquina sabrá, antes de iniciar la producción, si se está empleando el inductor adecuado para el programa de mecanizado seleccionado y en qué estado se encuentra la herramienta. Para ello, el sistema lee datos de rendimiento importantes, como la vida útil restante y los intervalos de mantenimiento pendientes, registrados en un chip RFID en la herramienta y los guarda de forma temporal. Una vez finalizado el proceso, el chip se sobrescribe con nueva información. Para esto hay disponible una nueva unidad de lectura y escritura en el sistema conectado a la máquina. En caso de defectos de la herramienta o de errores, el proceso ya no se inicia. "Sin embargo, las posibilidades van incluso más allá", comenta Endmann. "La máquina puede recibir información de las tolerancias de fabricación de la herramienta y, en caso necesario, reajustar sus eje de forma autónoma. De esta manera, el sistema mejora la calidad de mecanizado de forma adicional".
¿Qué cantidad de corriente fluye a través de la pieza?
Más calidad y menos fallos de proceso también son el resultado del segundo nuevo módulo dentro del eQC: en el futuro será posible medir la corriente en el pie del inductor mientras la producción está en marcha. Normalmente, estos valores de energía solo se miden en el inversor desde el que fluye la corriente a la herramienta. Por primera vez, el nuevo sistema informa de la cantidad de corriente que "llega" realmente a la herramienta. ¿Por qué es tan importante esta diferencia? "Solo de esta manera podemos saber con precisión la magnitud del flujo magnético que genera el inductor y que fluye a través de la pieza. Este valor depende directamente de la geometría de la herramienta y la pieza, así como de otros factores. Una medición en el inversor no se ve afectada por estos factores, por lo que no es suficientemente precisa. Ahora determinamos aquellos datos que se generan directamente en el lugar en el que se produce el valor añadido y los integramos en la monitorización del proceso", explica Endmann. Por el contrario, esto significa que el calentamiento de la pieza se monitoriza de manera mucho más exacta, que el proceso de templado se controla de forma más precisa y que, como consecuencia, la calidad de la pieza es mucho mayor.
¿Cómo se desarrolla la calidad del medio de enfriamiento brusco?
Un factor importante para la calidad y la estabilidad del proceso de templado es también el estado del medio de enfriamiento empleado, el cual cambia durante el proceso, ya que las cadenas de polímeros que contiene se rompen por efecto de la luz y el calor. Como consecuencia, el medio de enfriamiento pierde la tensión superficial requerida. "Por ello, es indispensable comprobar periódicamente la calidad del medio de enfriamiento. Actualmente, esto aún tiene lugar a menudo midiendo el índice de refracción. Sin embargo, esto no ofrece información acerca del estado de la cadena de polímeros, por lo que es un método demasiado impreciso. A partir de ahora empleamos un nuevo sensor, el cual monitoriza la viscosidad del medio de enfriamiento con la ayuda de ultrasonidos, lo que proporciona información muy precisa acerca de la calidad", comenta Endmann acerca del tercer nuevo módulo dentro del eQC. De esta manera se incrementa la seguridad en la producción de componentes complejos con muchos cantos y taladros, ya que existe la tendencia a que se generen fisuras cuando se emplea un medio de enfriamiento brusco.
Un amplio paquete para una mayor calidad y seguridad
En conjunto, los especialistas en inducción del sur de Alemania se encuentran en una óptima posición con este paquete de prestaciones. Todos los elementos eQC están basados los unos en los otros y se complementan: antes del inicio de la producción se comprueba la herramienta empleada y se registra su estado. Durante el proceso tiene lugar una medición de corriente de alta precisión directamente en la herramienta. Al mismo tiempo, un sensor comprueba constantemente la calidad del medio de enfriamiento brusco. Otros componentes estándar, como el controlador de energía, complementan la amplia oferta. "La producción industrial de nuestra época cambia muy rápidamente", explica Endmann para finalizar. "El concepto de la Industria 4.0 es el que indica la dirección a seguir: la producción no solo debe garantizar una calidad cada vez mayor, sino que esta calidad y su correspondiente proceso deben también documentarse ampliamente al mismo tiempo. Con las amplias medidas eQC garantizamos ambas cosas".
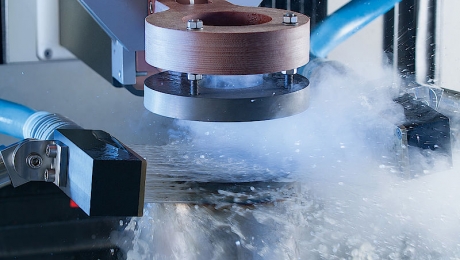
Los planificadores de la producción en la industria automotriz persiguen, cada vez más, una estrategia de "cero errores", en la medida en la que sea posible, ya que la complejidad técnica de los vehículos se ha incrementado enormemente en los últimos años. La consecuencia de ello son requisitos cada vez más exigentes, lo que supone un incremento del número de fuentes de error en la producción, como demuestran claramente las frecuentes campañas de llamada a taller de los últimos años. Esto hace necesario una monitorización de la calidad aún más amplia para muchos proveedores y fabricantes de equipos originales. Los procesos de tratamiento térmico también se ven especialmente afectados por ello, ya que tienen gran influencia en la estabilidad de componentes importantes. En este contexto, los especialistas en inducción de eldec renuevan su compromiso con todo lo relacionado con la monitorización de la calidad de las máquinas de templado inductivo: el "eldec Quality Control" abarca un paquete completo de nuevos ulos, con los que es posible optimizar la seguridad del proceso. Los componentes están basados los unos en los otros y se complementan. En combinación, garantizan a los usuarios un proceso de templado con una amplia monitorización.
Las cifras son cada vez más altas: de acuerdo con el instituto Center of Automotive Management (CAM) en Bergisch Gladbach, Alemania, solamente en EE. UU. se llamaron a taller más de 45 millones de vehículo el año pasado. "Problemas de seguridad", según el CAM, son la causa de ello. En dos años fue necesario comprobar y reparar en talleres más de 108 millones de vehículos en EE. UU. Esto supone enormes costos, los cuales tienen diferentes causas: los procesos de producción no seguros juegan aquí un papel central. El "eldec Quality Control" (eQC) sirve de ejemplo para evidenciar el esfuerzo que la ingeniería mecánica está haciendo para implantar un aseguramiento de la calidad a un nivel muy alto. Los especialistas de la inducción con sede en Dornstetten, cerca de Freudenstadt, Alemania, han dividido su paquete de medidas en dos áreas: "monitorización eléctrica" y "monitorización mecánica". Entre estas medidas se encuentran tres módulos completamente nuevos, los cuales contribuyen al aseguramiento de la calidad del proceso de templado: una detección de herramienta mediante un chip RFID, la medición continua de la tensión en el inductor y la monitorización del medio de enfriamiento brusco con ayuda de un sensor. "En total, mediante estas y otras medidas eQC se recoge una gran cantidad de datos, todos los cuales se guardan para compararlos con diferentes valores de referencia. En caso de desviaciones, la máquina informa del problema y detiene el proceso en determinadas circunstancias", explica Andreas Endmann, director del departamento de ventas tecnológicas para sistemas de templado de eldec. "Una mayor seguridad del proceso y una mejor monitorización de la calidad son casi impensables".
¿Se ha empleado la herramienta correcta?
La detección de herramientas sirve como ejemplo en la práctica: en el futuro, la máquina sabrá, antes de iniciar la producción, si se está empleando el inductor adecuado para el programa de mecanizado seleccionado y en qué estado se encuentra la herramienta. Para ello, el sistema lee datos de rendimiento importantes, como la vida útil restante y los intervalos de mantenimiento pendientes, registrados en un chip RFID en la herramienta y los guarda de forma temporal. Una vez finalizado el proceso, el chip se sobrescribe con nueva información. Para esto hay disponible una nueva unidad de lectura y escritura en el sistema conectado a la máquina. En caso de defectos de la herramienta o de errores, el proceso ya no se inicia. "Sin embargo, las posibilidades van incluso más allá", comenta Endmann. "La máquina puede recibir información de las tolerancias de fabricación de la herramienta y, en caso necesario, reajustar sus eje de forma autónoma. De esta manera, el sistema mejora la calidad de mecanizado de forma adicional".
¿Qué cantidad de corriente fluye a través de la pieza?
Más calidad y menos fallos de proceso también son el resultado del segundo nuevo módulo dentro del eQC: en el futuro será posible medir la corriente en el pie del inductor mientras la producción está en marcha. Normalmente, estos valores de energía solo se miden en el inversor desde el que fluye la corriente a la herramienta. Por primera vez, el nuevo sistema informa de la cantidad de corriente que "llega" realmente a la herramienta. ¿Por qué es tan importante esta diferencia? "Solo de esta manera podemos saber con precisión la magnitud del flujo magnético que genera el inductor y que fluye a través de la pieza. Este valor depende directamente de la geometría de la herramienta y la pieza, así como de otros factores. Una medición en el inversor no se ve afectada por estos factores, por lo que no es suficientemente precisa. Ahora determinamos aquellos datos que se generan directamente en el lugar en el que se produce el valor añadido y los integramos en la monitorización del proceso", explica Endmann. Por el contrario, esto significa que el calentamiento de la pieza se monitoriza de manera mucho más exacta, que el proceso de templado se controla de forma más precisa y que, como consecuencia, la calidad de la pieza es mucho mayor.
¿Cómo se desarrolla la calidad del medio de enfriamiento brusco?
Un factor importante para la calidad y la estabilidad del proceso de templado es también el estado del medio de enfriamiento empleado, el cual cambia durante el proceso, ya que las cadenas de polímeros que contiene se rompen por efecto de la luz y el calor. Como consecuencia, el medio de enfriamiento pierde la tensión superficial requerida. "Por ello, es indispensable comprobar periódicamente la calidad del medio de enfriamiento. Actualmente, esto aún tiene lugar a menudo midiendo el índice de refracción. Sin embargo, esto no ofrece información acerca del estado de la cadena de polímeros, por lo que es un método demasiado impreciso. A partir de ahora empleamos un nuevo sensor, el cual monitoriza la viscosidad del medio de enfriamiento con la ayuda de ultrasonidos, lo que proporciona información muy precisa acerca de la calidad", comenta Endmann acerca del tercer nuevo módulo dentro del eQC. De esta manera se incrementa la seguridad en la producción de componentes complejos con muchos cantos y taladros, ya que existe la tendencia a que se generen fisuras cuando se emplea un medio de enfriamiento brusco.
Un amplio paquete para una mayor calidad y seguridad
En conjunto, los especialistas en inducción del sur de Alemania se encuentran en una óptima posición con este paquete de prestaciones. Todos los elementos eQC están basados los unos en los otros y se complementan: antes del inicio de la producción se comprueba la herramienta empleada y se registra su estado. Durante el proceso tiene lugar una medición de corriente de alta precisión directamente en la herramienta. Al mismo tiempo, un sensor comprueba constantemente la calidad del medio de enfriamiento brusco. Otros componentes estándar, como el controlador de energía, complementan la amplia oferta. "La producción industrial de nuestra época cambia muy rápidamente", explica Endmann para finalizar. "El concepto de la Industria 4.0 es el que indica la dirección a seguir: la producción no solo debe garantizar una calidad cada vez mayor, sino que esta calidad y su correspondiente proceso deben también documentarse ampliamente al mismo tiempo. Con las amplias medidas eQC garantizamos ambas cosas".
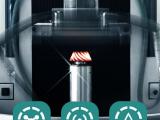