Eine Maschine, die auf allen Ebenen überzeugt
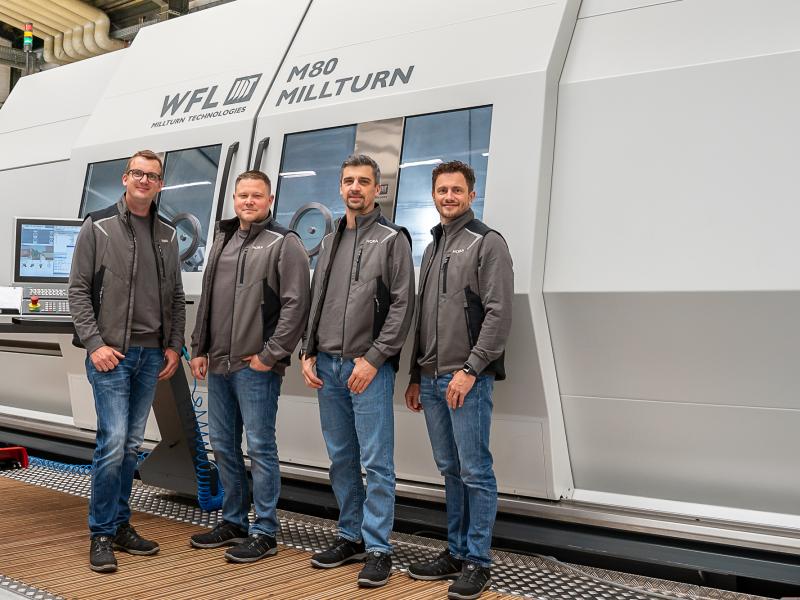
Mehrere Maschinenhersteller wurden in Betracht gezogen, doch schlussendlich konnte WFL das deutsche Familienunternehmen in allen Punkten überzeugen. Besonders der Service und die Erreichbarkeit waren ausschlaggebend. Welche Kriterien für HORA bei der Entscheidung noch wichtig waren und wie WFL das erfolgreich umsetzen konnte, werden im Folgenden erläutert.
HORA ist ein mittelständisches Familienunternehmen mit Sitz im ostwestfälischen Schloß Holte-Stukenbrock und beschäftigt aktuell rund 300 Mitarbeiterinnen und Mitarbeiter. Das Engineering und die Produktion finden an diesem Standort statt und werden von einer Vertriebsniederlassung in Shanghai und diversen Vertriebspartnern weltweit unterstützt. Seit der Gründung 1967 durch Georg Dresselhaus konzentriert sich das Unternehmen auf die Entwicklung, Konstruktion und Herstellung von innovativen Regelarmaturen und Stellantrieben. Durch die konsequente Ausrichtung auf die Geschäftsfelder Power Generation, Gas Applications, Process- und Building Technology bedient HORA sehr spezifisch die Kundenbedürfnisse. HORA liefert Regelungstechnik passgenau für die jeweiligen Anforderungen und sichert damit nachhaltig einen reibungslosen und effizienten Betrieb der Anlagen Ihrer Kund*innen.
Der Jahresumsatz im Geschäftsjahr 2023 lag bei 50 Millionen Euro. Der komplette Unternehmensgewinn wird bei HORA reinvestiert, daher gehört die modernste Technik zur Betriebsausstattung. In den letzten fünf Jahren wurden über 10 Millionen Euro in die Fertigung investiert. Die Investition in ein WFL-Bearbeitungszentrum ist die größte Einzelinvestition in eine Maschine seit Unternehmensgründung. Gesellschafter Prof. Dr. Dieter Dresselhaus legt einen starken Fokus auf Prozessinnovation und sichert somit über Jahrzehnte den langfristigen Unternehmenserfolg.
Die Herausforderung
Die Fertigungsstrategie der Komplettbearbeitung steht seit 2009 im Fokus von HORA – jedoch begrenzt durch Bauteilgröße und -gewicht. In den vergangenen Jahren hat die Anzahl der zu fertigenden Teile, die aus diesem Grund nicht in Komplettbearbeitung hergestellt werden konnten, zugenommen. Zudem entwickelt sich der Markt hin zu schwer zerspanbaren Werkstoffen, die eine zunehmende Herausforderung darstellten. Es wurde also eine Maschine mit entsprechendem Spanraum und -leistung benötigt.
Seit 2015 fokussiert sich das Unternehmen HORA auf die digitale Transformation des gesamten Auftragsdurchlaufs, von der Kundenanfrage bis zur Auslieferung und darüber hinaus. In diesen Jahren wurden unter anderem ein ERP-System mit integriertem APS, ein PDM-System, ein Produktkonfigurator und ein digitales Versandmanagement eingeführt. Alle Systeme sind vernetzt.
Mit der Investition in ein Bearbeitungszentrum sollten neben den Herausforderungen in der Schwerzerspanung die letzten Puzzlesteine für einen vollständig digitalisierten State of the Art Prozess im Fertigungsumfeld realisiert werden.
„Das Bild der vollständigen digitalen Vernetzung bei HORA wollten wir durch die Implementierung und digitalen Anbindung der, aktuell aus unserer Sicht, besten Maschine für unsere Anforderungen realisieren“, sagt Prokurist und Mitglied der Geschäftsleitung Eduard Schmidt. Er sagt weiter: „Wir brauchten jemanden, der uns technologisch, beim Setzen eines neuen Maßstabs im digitalen Prozess, partnerschaftlich unterstützt und uns hilft, unser Bild in die Realität zu bringen. WFL war dafür aus unserer Sicht die absolut richtige Entscheidung, da die Unternehmen HORA und WFL Wert darauf legen, gemeinsam die optimale Lösung für den jeweiligen Kunden umzusetzen. Mit einem einheitlichen Verständnis war somit die Grundlage gesetzt, gemeinsam einen neuen Maßstab zu setzen“, betont Schmidt.
Die Entscheidung für eine WFL
Mehrere Gründe waren ausschlaggebend für die Entscheidung für eine MILLTURN. Vom ersten Gespräch bis zum Projektabschluss und jetzt weit darüber hinaus, fühlt sich HORA bei WFL gut aufgehoben. HORA lobt im Gespräch mit WFL das gesamte Projektteam und betont, dass jede Zusage eingehalten oder sogar übertroffen wurde. „Wir waren mehrfach bei WFL in Linz zu Besuch und konnten uns selbst von dem herausragenden Know-How überzeugen. Vor Ort lagernde Werkstücke mit ähnlichem Material, also schwer zerspanbare und vor allem geometrisch herausfordernde, wurden bereits gefertigt. Die Referenzen von WFL im Einsatz sprachen dabei für sich. Der Fokus bei WFL liegt auf der Technologie und Prozessintegration “, sagt Andreas Petker, Teamleiter Produktion bei HORA.
Außerdem überzeugte WFL mit der garantieren Service- und Ersatzteilverfügbarkeit. Mit WFL hat HORA einen Partner, der aufgrund der räumlichen Nähe rasch verfügbar ist. Das Risiko eines möglichen Produktionsausfalls wurde somit minimiert.
Nicht zu vergessen ist die Dreh-Bohr-Fräseinheit als Herzstück der Maschine. Ausschlaggebend war der Fakt, dass diese komplett im Haus WFL gefertigt wird. Ein Alleinstellungsmerkmal von WFL, welches die Verantwortlichen von HORA überzeugte.
Als ein weiteres Alleinstellungsmerkmal war die Systembohrstange entscheidend, die HORA aufgrund der Geometrie der zu fertigenden Bauteile einen Mehrwert in Flexibilität und Kosten bietet.
HORA baut die Mehrmaschinenbedienung in der Einzelteilfertigung seit Jahren stark aus und wählt daher vorrangig Maschinen, die mit einer Siemens-Steuerung arbeiten. Somit bleibt das Handling maschinenübergreifend ähnlich und ist für die Mitarbeiter*innen leicht bedienbar.
Die Maschine begeistert seit Anfang des Jahres tagtäglich in der Anwendung. Die massive Bauweise und die Bearbeitungsleistung sind bemerkenswert. „Die Bearbeitungen in dieser Größenordnung sind nicht neu für uns, aber die Zerspanleistung ist bemerkenswert und überzeugend! Schon bei der Abnahme der Maschine wurde die Zerspanleistung überragend präsentiert, als der 160er Wendeplattenbohrer mit zwei Tonnen Vorschubkraft den warmfesten Edelbaustahl (1.7335) mühelos und ohne jegliche Vibration an der Maschinenverkleidung zerspant hat. In solchen Momenten greife ich immer gerne an die Tür, aber es war keinerlei Vibration zu spüren“, betont Michael Beiwinkel, Leitung Produktions- und Gebäudetechnik. Die Stabilität und der massive Aufbau überzeugten. Ein weiterer Pluspunkt ist, dass die Antriebskräfte nicht zu 100 Prozent benötigt werden. Trotz schwieriger Werkstoffe und kräftezehrender Werkzeuge sind immer noch Antriebsreserven vorhanden und das bei einem sehr hohen Spanvolumen, das abgetragen wird. Im Januar 2024 wurde die Maschine bei HORA in Betrieb genommen.
Ergonomisches Arbeiten
Als innovatives Unternehmen legt HORA höchsten Wert auf optimale Arbeitsplatzgestaltung für ihre Mitarbeitenden. Für einen optimalen Zugang zu den Werkstücken in der Bearbeitung wurde die MILLTURN in den vorhandenen Hallenboden versenkt. „Auch hier waren wir von WFL begeistert, es benötigte nicht mal eine Sonderlösung, da die Maschine vom Grundsatz für optimale ergonomische Bedingungen ausgelegt ist“, sagt Teamleiter Produktion Sascha Brechmann. Zuerst wurde eine ein Meter tiefe Grube gegraben, dann folgte der notwendige Aufbau und nun ist die MILLTURN um 400mm tiefergestellt. Der Ablagebereich vor der Maschine wurde durch eine Stahlschweißkonstruktion so ausgeführt, dass man ein Werkstück mit bis zu sechs Tonnen ohne Probleme ablegen kann. Der Arbeitsplatz bei der MILLTURN, aber auch bei allen anderen Maschinen in der Halle von HORA, weisen Arbeitssicherheit und eine großartige Ergonomie auf. Es gibt im Boden integrierte Holzböden für ein ergonomisch optimales Arbeitsumfeld. Ebenso gibt es keine Stufen und somit einen ebenerdigen Zutritt, der die Rutschgefahr erheblich reduziert.
Die Maschine wird zurzeit in Zweischicht betrieben. Vier Mitarbeitende haben das WFL-Schulungsprogramm in Linz und mit dem Techniker direkt an der Maschine bei HORA durchlaufen und bedienen die WFL-Maschine nun selbstständig. Bereits acht Wochen nach der Abnahme der Maschine arbeitete die M80 MILLTURN bei Einzelteilen teilweise ohne einen direkt zugeordneten Maschinenbediener. Bei Bauteilen, die eine längere Bearbeitungszeit aufweisen, läuft die Maschine insbesondere über Nacht ohne Aufsicht.
Auf der Maschine werden im Wesentlichen Ventilgehäuse, Lochscheiben, Lochkörbe und Kegel hergestellt. Diese hergestellten Teile kann man wiederum in jeglicher Art von Regelventilen für kundenindividuelle, anspruchsvolle Lösungen in den unterschiedlichsten Branchen finden.
Neue Maßstäbe in der digitalen Vernetzung
Mit der Entscheidung für die WFL gelingt HORA der Lückenschluss in der digitalen Transformation des Auftragsdurchlaufs. An den digitalen Prozess von Kundenanfrage bis zum Abschluss der Auftragskonstruktion schließt sich nun der Fertigungsprozess an. „Von der Anfrage im Angebot bis zum entstehenden Produkt haben wir jetzt alles digital - egal wo wir in der Fabrik sind“, sagt Schmidt.
Aus den durch die Auftragskonstruktion im PDM System abgelegten CAD Modellen erstellt das CAM Team den CAM Datensatz, welcher nach der Simulation im CrashGuard Studio im ShopFloor abgelegt wird.
„Die Kombination der Anwendungen im CAM und CrashGuard Studio gestaltet sich sehr spannend. Oft haben wir Bearbeitungen, wo es keine Maschinenzyklen gibt, und dann geht die Bearbeitung zuerst ins CAM“, so Sergej Kunz, Teamleiter CAM.
Anhand der im ShopFloor abgelegten Daten werden nun die benötigten Werkzeuge gerüstet und vermessen. Die ermittelten Werkzeugdaten werden ebenfalls im ShopFloor abgelegt. Mit einem aus ShopFloor generierten Datamatrix-Code kann das Werkzeug jederzeit identifiziert und gebucht werden.
Die komplette Fertigungssteuerung bei HORA übernimmt das integrierte APS im ERP. Plant das APS einen Fertigungsauftrag auf die WFL, werden alle Daten (NC-Programm aus dem CAM und Werkzeugdaten der Vermessung) aus dem ShopFloor auf die Maschine geladen. Während der Bearbeitung werden regelmäßig Messzyklen durchgeführt, um die Bauteilqualität zu garantieren. So entsteht ein digitaler Zwilling jedes gefertigten Bauteils.
„Durch die Messzyklen im Prozess konnten wir die Qualität unserer Werkstücke erheblich steigern“, sagt Sergej Kunz. Er sagt weiter: „Gerade bei den großen Bauteilen werden durch die Messzyklen erhebliche Effizienzgewinne erzielt. Allgemein konnten wir vorher gewisse Konturen im Bearbeitungsprozess nicht messen, was jetzt machbar ist. Durch die Messzyklen und den Kreuztaster können wir jetzt einfach sehr genau fertigen und das verschafft uns natürlich einen enormen zeitlichen und qualitativen Benefit.“
Schritte für die Zukunft
Das klare Bekenntnis des Gesellschafters Herrn Prof. Dr. Dieter Dresselhaus zum Standort Schloß Holte-Stukenbrock unterstreicht er seit Jahren mit der 100% Reinvestition aller Unternehmensgewinne deutlich. Dieses Handeln ermöglicht das Setzen neuer Maßstäbe in der Prozess- und Produktinnovation.
Die Produkte von HORA leisten einen wesentlichen Beitrag, um die Energiewende voranzutreiben. Daher rechnet das Unternehmen mit weiterhin steigender Nachfrage seiner Premiumprodukte. Aus diesem Grund steht die Effizienzsteigerung weiter im Fokus. Bei seinen Aktivitäten achtet das Unternehmen dabei stets auf die effiziente Nutzung von Energie und Ressourcen. „Wir achten darauf, dass die Beschaffung von Materialien nachhaltig ist. Luftfracht und Schiff werden so weit wie möglich vermieden. Bei unserem gesamten Beschaffungsvolumen von 17 Millionen Euro belaufen sich nur rund 1,5 Millionen Euro auf Waren aus Asien. Das unterstreicht auch unser weitgehendes regionales Einkaufen und unsere vielen partnerschaftlichen Verhältnisse in Deutschland und Europa“, betont Schmidt.
„Als Partner for Performance sehen wir unsere Stärke darin, die Kundenbedürfnisse zu verstehen und in Produkte für anspruchsvolle Regelungsaufgaben umzusetzen. Diese Ausrichtung haben wir auch bei WFL schon während der Verhandlungen zur Maschinenauslegung festgestellt. Das hat sich im Projektverlauf genauso bestätigt“, sagt Schmidt. Und meint weiter: „Wir haben definitiv den richtigen Partner gewählt. Die Werte der Firma sind mit Leben gefüllt, bei HORA wie bei WFL.“
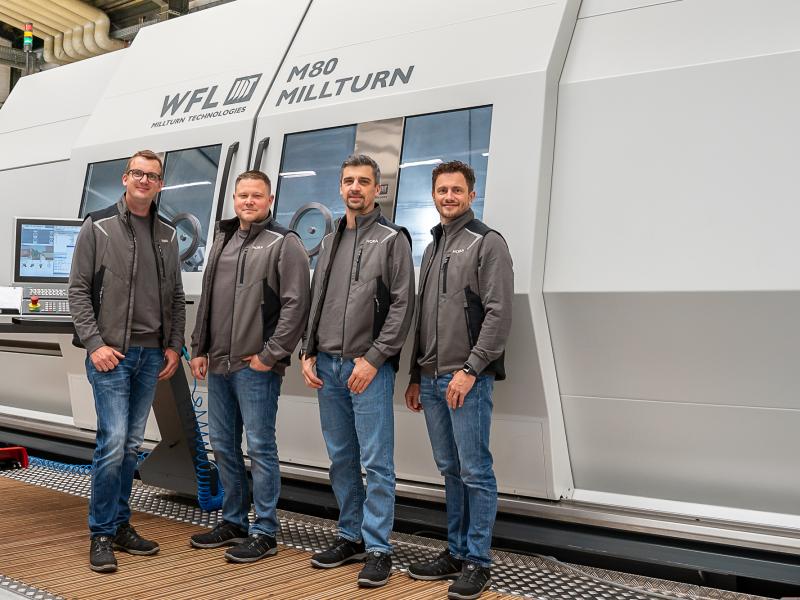
Mehrere Maschinenhersteller wurden in Betracht gezogen, doch schlussendlich konnte WFL das deutsche Familienunternehmen in allen Punkten überzeugen. Besonders der Service und die Erreichbarkeit waren ausschlaggebend. Welche Kriterien für HORA bei der Entscheidung noch wichtig waren und wie WFL das erfolgreich umsetzen konnte, werden im Folgenden erläutert.
HORA ist ein mittelständisches Familienunternehmen mit Sitz im ostwestfälischen Schloß Holte-Stukenbrock und beschäftigt aktuell rund 300 Mitarbeiterinnen und Mitarbeiter. Das Engineering und die Produktion finden an diesem Standort statt und werden von einer Vertriebsniederlassung in Shanghai und diversen Vertriebspartnern weltweit unterstützt. Seit der Gründung 1967 durch Georg Dresselhaus konzentriert sich das Unternehmen auf die Entwicklung, Konstruktion und Herstellung von innovativen Regelarmaturen und Stellantrieben. Durch die konsequente Ausrichtung auf die Geschäftsfelder Power Generation, Gas Applications, Process- und Building Technology bedient HORA sehr spezifisch die Kundenbedürfnisse. HORA liefert Regelungstechnik passgenau für die jeweiligen Anforderungen und sichert damit nachhaltig einen reibungslosen und effizienten Betrieb der Anlagen Ihrer Kund*innen.
Der Jahresumsatz im Geschäftsjahr 2023 lag bei 50 Millionen Euro. Der komplette Unternehmensgewinn wird bei HORA reinvestiert, daher gehört die modernste Technik zur Betriebsausstattung. In den letzten fünf Jahren wurden über 10 Millionen Euro in die Fertigung investiert. Die Investition in ein WFL-Bearbeitungszentrum ist die größte Einzelinvestition in eine Maschine seit Unternehmensgründung. Gesellschafter Prof. Dr. Dieter Dresselhaus legt einen starken Fokus auf Prozessinnovation und sichert somit über Jahrzehnte den langfristigen Unternehmenserfolg.
Die Herausforderung
Die Fertigungsstrategie der Komplettbearbeitung steht seit 2009 im Fokus von HORA – jedoch begrenzt durch Bauteilgröße und -gewicht. In den vergangenen Jahren hat die Anzahl der zu fertigenden Teile, die aus diesem Grund nicht in Komplettbearbeitung hergestellt werden konnten, zugenommen. Zudem entwickelt sich der Markt hin zu schwer zerspanbaren Werkstoffen, die eine zunehmende Herausforderung darstellten. Es wurde also eine Maschine mit entsprechendem Spanraum und -leistung benötigt.
Seit 2015 fokussiert sich das Unternehmen HORA auf die digitale Transformation des gesamten Auftragsdurchlaufs, von der Kundenanfrage bis zur Auslieferung und darüber hinaus. In diesen Jahren wurden unter anderem ein ERP-System mit integriertem APS, ein PDM-System, ein Produktkonfigurator und ein digitales Versandmanagement eingeführt. Alle Systeme sind vernetzt.
Mit der Investition in ein Bearbeitungszentrum sollten neben den Herausforderungen in der Schwerzerspanung die letzten Puzzlesteine für einen vollständig digitalisierten State of the Art Prozess im Fertigungsumfeld realisiert werden.
„Das Bild der vollständigen digitalen Vernetzung bei HORA wollten wir durch die Implementierung und digitalen Anbindung der, aktuell aus unserer Sicht, besten Maschine für unsere Anforderungen realisieren“, sagt Prokurist und Mitglied der Geschäftsleitung Eduard Schmidt. Er sagt weiter: „Wir brauchten jemanden, der uns technologisch, beim Setzen eines neuen Maßstabs im digitalen Prozess, partnerschaftlich unterstützt und uns hilft, unser Bild in die Realität zu bringen. WFL war dafür aus unserer Sicht die absolut richtige Entscheidung, da die Unternehmen HORA und WFL Wert darauf legen, gemeinsam die optimale Lösung für den jeweiligen Kunden umzusetzen. Mit einem einheitlichen Verständnis war somit die Grundlage gesetzt, gemeinsam einen neuen Maßstab zu setzen“, betont Schmidt.
Die Entscheidung für eine WFL
Mehrere Gründe waren ausschlaggebend für die Entscheidung für eine MILLTURN. Vom ersten Gespräch bis zum Projektabschluss und jetzt weit darüber hinaus, fühlt sich HORA bei WFL gut aufgehoben. HORA lobt im Gespräch mit WFL das gesamte Projektteam und betont, dass jede Zusage eingehalten oder sogar übertroffen wurde. „Wir waren mehrfach bei WFL in Linz zu Besuch und konnten uns selbst von dem herausragenden Know-How überzeugen. Vor Ort lagernde Werkstücke mit ähnlichem Material, also schwer zerspanbare und vor allem geometrisch herausfordernde, wurden bereits gefertigt. Die Referenzen von WFL im Einsatz sprachen dabei für sich. Der Fokus bei WFL liegt auf der Technologie und Prozessintegration “, sagt Andreas Petker, Teamleiter Produktion bei HORA.
Außerdem überzeugte WFL mit der garantieren Service- und Ersatzteilverfügbarkeit. Mit WFL hat HORA einen Partner, der aufgrund der räumlichen Nähe rasch verfügbar ist. Das Risiko eines möglichen Produktionsausfalls wurde somit minimiert.
Nicht zu vergessen ist die Dreh-Bohr-Fräseinheit als Herzstück der Maschine. Ausschlaggebend war der Fakt, dass diese komplett im Haus WFL gefertigt wird. Ein Alleinstellungsmerkmal von WFL, welches die Verantwortlichen von HORA überzeugte.
Als ein weiteres Alleinstellungsmerkmal war die Systembohrstange entscheidend, die HORA aufgrund der Geometrie der zu fertigenden Bauteile einen Mehrwert in Flexibilität und Kosten bietet.
HORA baut die Mehrmaschinenbedienung in der Einzelteilfertigung seit Jahren stark aus und wählt daher vorrangig Maschinen, die mit einer Siemens-Steuerung arbeiten. Somit bleibt das Handling maschinenübergreifend ähnlich und ist für die Mitarbeiter*innen leicht bedienbar.
Die Maschine begeistert seit Anfang des Jahres tagtäglich in der Anwendung. Die massive Bauweise und die Bearbeitungsleistung sind bemerkenswert. „Die Bearbeitungen in dieser Größenordnung sind nicht neu für uns, aber die Zerspanleistung ist bemerkenswert und überzeugend! Schon bei der Abnahme der Maschine wurde die Zerspanleistung überragend präsentiert, als der 160er Wendeplattenbohrer mit zwei Tonnen Vorschubkraft den warmfesten Edelbaustahl (1.7335) mühelos und ohne jegliche Vibration an der Maschinenverkleidung zerspant hat. In solchen Momenten greife ich immer gerne an die Tür, aber es war keinerlei Vibration zu spüren“, betont Michael Beiwinkel, Leitung Produktions- und Gebäudetechnik. Die Stabilität und der massive Aufbau überzeugten. Ein weiterer Pluspunkt ist, dass die Antriebskräfte nicht zu 100 Prozent benötigt werden. Trotz schwieriger Werkstoffe und kräftezehrender Werkzeuge sind immer noch Antriebsreserven vorhanden und das bei einem sehr hohen Spanvolumen, das abgetragen wird. Im Januar 2024 wurde die Maschine bei HORA in Betrieb genommen.
Ergonomisches Arbeiten
Als innovatives Unternehmen legt HORA höchsten Wert auf optimale Arbeitsplatzgestaltung für ihre Mitarbeitenden. Für einen optimalen Zugang zu den Werkstücken in der Bearbeitung wurde die MILLTURN in den vorhandenen Hallenboden versenkt. „Auch hier waren wir von WFL begeistert, es benötigte nicht mal eine Sonderlösung, da die Maschine vom Grundsatz für optimale ergonomische Bedingungen ausgelegt ist“, sagt Teamleiter Produktion Sascha Brechmann. Zuerst wurde eine ein Meter tiefe Grube gegraben, dann folgte der notwendige Aufbau und nun ist die MILLTURN um 400mm tiefergestellt. Der Ablagebereich vor der Maschine wurde durch eine Stahlschweißkonstruktion so ausgeführt, dass man ein Werkstück mit bis zu sechs Tonnen ohne Probleme ablegen kann. Der Arbeitsplatz bei der MILLTURN, aber auch bei allen anderen Maschinen in der Halle von HORA, weisen Arbeitssicherheit und eine großartige Ergonomie auf. Es gibt im Boden integrierte Holzböden für ein ergonomisch optimales Arbeitsumfeld. Ebenso gibt es keine Stufen und somit einen ebenerdigen Zutritt, der die Rutschgefahr erheblich reduziert.
Die Maschine wird zurzeit in Zweischicht betrieben. Vier Mitarbeitende haben das WFL-Schulungsprogramm in Linz und mit dem Techniker direkt an der Maschine bei HORA durchlaufen und bedienen die WFL-Maschine nun selbstständig. Bereits acht Wochen nach der Abnahme der Maschine arbeitete die M80 MILLTURN bei Einzelteilen teilweise ohne einen direkt zugeordneten Maschinenbediener. Bei Bauteilen, die eine längere Bearbeitungszeit aufweisen, läuft die Maschine insbesondere über Nacht ohne Aufsicht.
Auf der Maschine werden im Wesentlichen Ventilgehäuse, Lochscheiben, Lochkörbe und Kegel hergestellt. Diese hergestellten Teile kann man wiederum in jeglicher Art von Regelventilen für kundenindividuelle, anspruchsvolle Lösungen in den unterschiedlichsten Branchen finden.
Neue Maßstäbe in der digitalen Vernetzung
Mit der Entscheidung für die WFL gelingt HORA der Lückenschluss in der digitalen Transformation des Auftragsdurchlaufs. An den digitalen Prozess von Kundenanfrage bis zum Abschluss der Auftragskonstruktion schließt sich nun der Fertigungsprozess an. „Von der Anfrage im Angebot bis zum entstehenden Produkt haben wir jetzt alles digital - egal wo wir in der Fabrik sind“, sagt Schmidt.
Aus den durch die Auftragskonstruktion im PDM System abgelegten CAD Modellen erstellt das CAM Team den CAM Datensatz, welcher nach der Simulation im CrashGuard Studio im ShopFloor abgelegt wird.
„Die Kombination der Anwendungen im CAM und CrashGuard Studio gestaltet sich sehr spannend. Oft haben wir Bearbeitungen, wo es keine Maschinenzyklen gibt, und dann geht die Bearbeitung zuerst ins CAM“, so Sergej Kunz, Teamleiter CAM.
Anhand der im ShopFloor abgelegten Daten werden nun die benötigten Werkzeuge gerüstet und vermessen. Die ermittelten Werkzeugdaten werden ebenfalls im ShopFloor abgelegt. Mit einem aus ShopFloor generierten Datamatrix-Code kann das Werkzeug jederzeit identifiziert und gebucht werden.
Die komplette Fertigungssteuerung bei HORA übernimmt das integrierte APS im ERP. Plant das APS einen Fertigungsauftrag auf die WFL, werden alle Daten (NC-Programm aus dem CAM und Werkzeugdaten der Vermessung) aus dem ShopFloor auf die Maschine geladen. Während der Bearbeitung werden regelmäßig Messzyklen durchgeführt, um die Bauteilqualität zu garantieren. So entsteht ein digitaler Zwilling jedes gefertigten Bauteils.
„Durch die Messzyklen im Prozess konnten wir die Qualität unserer Werkstücke erheblich steigern“, sagt Sergej Kunz. Er sagt weiter: „Gerade bei den großen Bauteilen werden durch die Messzyklen erhebliche Effizienzgewinne erzielt. Allgemein konnten wir vorher gewisse Konturen im Bearbeitungsprozess nicht messen, was jetzt machbar ist. Durch die Messzyklen und den Kreuztaster können wir jetzt einfach sehr genau fertigen und das verschafft uns natürlich einen enormen zeitlichen und qualitativen Benefit.“
Schritte für die Zukunft
Das klare Bekenntnis des Gesellschafters Herrn Prof. Dr. Dieter Dresselhaus zum Standort Schloß Holte-Stukenbrock unterstreicht er seit Jahren mit der 100% Reinvestition aller Unternehmensgewinne deutlich. Dieses Handeln ermöglicht das Setzen neuer Maßstäbe in der Prozess- und Produktinnovation.
Die Produkte von HORA leisten einen wesentlichen Beitrag, um die Energiewende voranzutreiben. Daher rechnet das Unternehmen mit weiterhin steigender Nachfrage seiner Premiumprodukte. Aus diesem Grund steht die Effizienzsteigerung weiter im Fokus. Bei seinen Aktivitäten achtet das Unternehmen dabei stets auf die effiziente Nutzung von Energie und Ressourcen. „Wir achten darauf, dass die Beschaffung von Materialien nachhaltig ist. Luftfracht und Schiff werden so weit wie möglich vermieden. Bei unserem gesamten Beschaffungsvolumen von 17 Millionen Euro belaufen sich nur rund 1,5 Millionen Euro auf Waren aus Asien. Das unterstreicht auch unser weitgehendes regionales Einkaufen und unsere vielen partnerschaftlichen Verhältnisse in Deutschland und Europa“, betont Schmidt.
„Als Partner for Performance sehen wir unsere Stärke darin, die Kundenbedürfnisse zu verstehen und in Produkte für anspruchsvolle Regelungsaufgaben umzusetzen. Diese Ausrichtung haben wir auch bei WFL schon während der Verhandlungen zur Maschinenauslegung festgestellt. Das hat sich im Projektverlauf genauso bestätigt“, sagt Schmidt. Und meint weiter: „Wir haben definitiv den richtigen Partner gewählt. Die Werte der Firma sind mit Leben gefüllt, bei HORA wie bei WFL.“